TallWood Design Institute reaches out
Based at the College of Forestry at Oregon State University, the TallWood Design Institute (TDI) is the nation’s leading research collaborative focused on the advancement of structural wood products and mass timber design.
The institute represents a unique interdisciplinary partnership between OSU’s Colleges of Forestry and Engineering and the University of Oregon’s College of Design. The institute is at the forefront of mass timber research and real-world relevance. Its core tenets are the importance of industry collaboration, through outreach, education and feedback from professionals.
“Our goal is to conduct meaningful research and engage with the building community to help validate and highlight how these products and building systems work,” says Outreach Coordinator Evan Schmidt.
During FY 2017 and 2018, TDI focused on outreach by developing avenues of collaboration with community partners including product development, testing with manufacturers, educational seminars for students and designers and applied research projects with engineering firms.
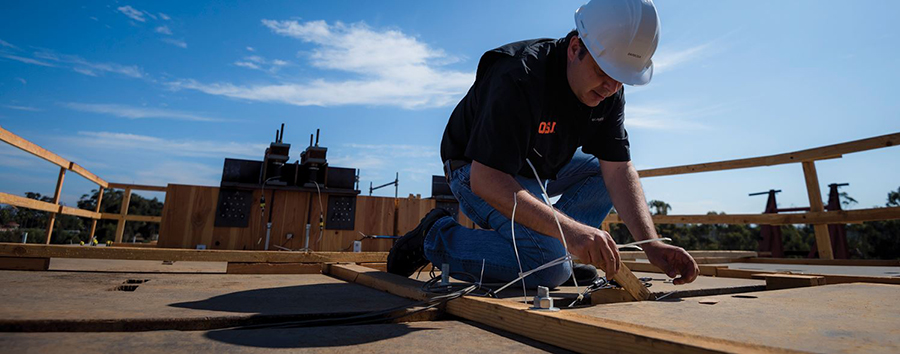
Connecting with industry
TDI worked with the Freres Lumber Company in Lyons to test and develop an entirely new engineered wood product, mass plywood panels (MPP), in 2017 and 2018. TDI funded the second-phase of Freres’s testing, and continuing work with Freres includes optimizing MPP’s layup through modeling, structural testing, life cycle analysis, acoustics and architectural design applications.
MPP, like CLT, can be used as a substitute for conventional building materials. Now certified by the APA for structural use, MPP was installed for the first time in the U.S. as sheathing on Oregon State’s new A.A. “Red” Emmerson Advanced Wood Products Laboratory in Corvallis.
“We are a good example of a family business working within our rural community to come up with something new and innovative,” Tyler Freres says. “It’s also been great to have the experts and the researchers at OSU and the TallWood Design Institute working with us on this project. We have a very close relationship, and appreciate all the extra hands involved in producing MPP.”
Advanced wood products for the next generation
Judith Sheine, TDI’s director of design and professor of architecture at the University of Oregon, focuses on another application for MPP. MPP-based modular construction was the focus of her most recent undergraduate architecture and engineering design studio. Focusing on mass timber applications allowed Sheine to partner with Modular Building Systems and Clackamas County to discuss a partnership project using MPP for Oregon highway rest stops.
The modular MPP project isn’t the first time Sheine’s mass timber design studio has resulted in a public-private partnership. SRG Architecture and KPFF Engineering worked intimately with TDI and the City of Springfield on a CLT parking garage after it was the focus on of Sheine’s studio classes in 2016.
Architects and engineers across the United States have expressed interest in creating similar structures. Lane County has also participated in the design studio process, and hopes to build its new court house from mass timber based on one of the award-winning designs that came out of the classroom.
Schmidt says he’s excited about continuing to engage with TDI’s industry partners.
“Research advancing mass timber is a time sensitive effort,” he says. “The private sector moves at a different pace and under different logistics than academia, so it’s essential that we continue to engage the design community. That’s what keeps us relevant, while our research is what lends credence to mass timber as a solution.”
New facilities will aid industry tests
TDI’s access to state-of-the-art testing facilities helps it accomplish its innovative research. The new A.A. “Red” Emmerson Advanced Wood Products Laboratory builds on the strengths of existing facilities. The lab is scheduled for completion in summer 2019, and will have both a three-story structural testing bay, as well as an advanced manufacturing lab. In addition to research applications, the manufacturing lab will contain a hands-on educational space for students, skilled workers and design professionals looking to learn more about mass timber applications.
Another research space in the design and development phase is a full-scale acoustic-testing facility that will be built in the Willamette Valley. The lab will be one of only a few certified acoustics testing facilities along the West Coast, and will offer TDI’s industry partners the opportunity to rapidly test and prototype mass timber assemblies based on their acoustic properties. The lack of a facility like this is often a limiting factor when it comes to utilizing mass timber, and TDI is excited to fill that gap for its industry partners.
Portland meetups a success
Part of TDI’s outreach approach includes holding educational and networking events geared toward bringing various stakeholders together to learn, collaborate and problem solve all things mass timber. To accomplish this, TDI hosts a monthly event in Portland called ‘Mass Timber Meetups.’ These are casual, network-focused events that are designed to stimulate discussion on a specific subject within the world of mass timber.
“We discuss topics like acoustics, fire, building information modeling (BIM) and more,” Schmidt says. “It’s a place where people who have worked with mass timber, or are just curious, can discuss their experience or ask questions.”
These conversations help to build a community around mass timber construction and educate construction professionals from a variety of areas. About 15-30 people from various backgrounds typically attend. These events are free and open to the public and will continue in 2019.